.jpg)
Credentials & Certifications:
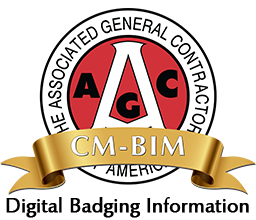
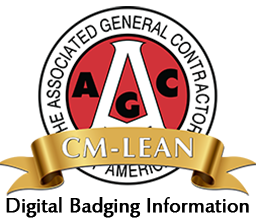
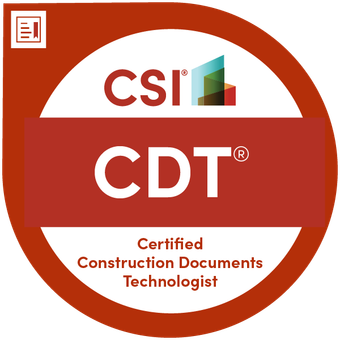
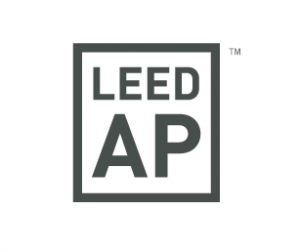
What Colleagues Say
""
-
Core Competencies
Providing expert consultation to help organizations plan, implement, and optimize their digital projects and assets.
AECO Digital Strategy & Implementation
From technology roadmapping to full-scale implementation, we guide your organization through every step of its digital journey.
National & Organizational Standards
Leverage our leadership in developing National BIM/CAD Standards (NBIMS-US™, NCS) to build a robust digital framework for your team.
Performance Improvement & Process Reengineering
We analyze your current workflows, identify bottlenecks, and reengineer processes for maximum efficiency and quality.
Technology Change Management
Ensure successful technology adoption with our proven change management strategies, focusing on people, processes, and tools.
BIM, VDC, & Digital Twins
Expert guidance on Building Information Modeling, Virtual Design & Construction, and the emerging field of Digital Twins.
Advisory, Training, & Development
Leverage decades of experience in corporate training and university-level course development for your teams.
Expert Witness Services
Dr. Fortune is qualified to serve as an expert witness in legal matters concerning the AECO industry. He is a proud member of the Round Table Group, which assists individuals and organizations in locating premier expert witnesses.
Government Contracting
AECO Digital Technologies is a registered small business committed to providing expert digital transformation services to federal, state, and local government agencies. We have a proven track record of supporting public sector projects and advancing national standards.
Past Performance Highlights
- **National Institute of Building Sciences (NIBS):** Led the National BIM Program as Executive Director, guiding the creation and evolution of U.S. digital standards.
- **U.S. Department of Veterans Affairs (VA):** Instrumental in developing and authoring key national standards, including the VA BIM Guide and Drawing Deliverable Requirements.
- **U.S. Army Corps of Engineers (USACE):** Ongoing collaboration on requirements documents and leadership within the USACE/Industry BIM/CIM Consortia.
Contracting Information
- UEI: YU6VHMEG9B37
- CAGE Code: 123E2
- Business Status: Small Business (SAM & SBA Registered)
NAICS Codes
Industry Insights & Thought Leadership
Sharing knowledge to advance the AECO industry. Explore articles, publications, and key presentations.
From the Host of AECO Tech Talk
Join Dr. Fortune on the AECO Tech Talk podcast, where he explores the latest trends and interviews leaders at the forefront of digital transformation in the built environment.
Unlocking 5D BIM: Why Cost Estimators Don’t Trust the Models (Yet)
An exploration into the barriers of 5D BIM adoption and the steps needed to build trust and integrate cost estimation with design models effectively.
Read Full Article →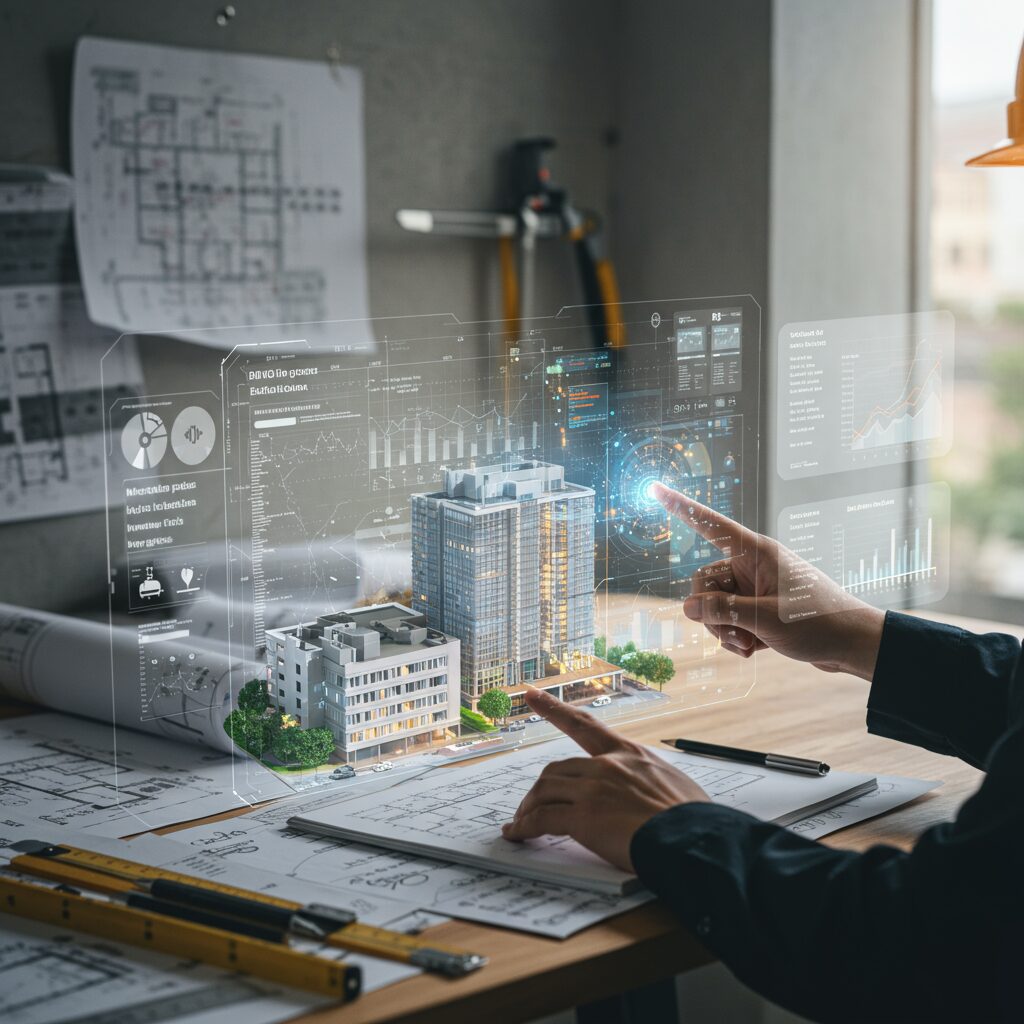
Upcoming Engagements
Past Engagements
Building Transformations
COAA
CURT
PROCORE
Ready to Transform Your Digital Processes?
Let's discuss how AECO Digital Technologies can help you achieve your goals. Schedule a complimentary consultation today.
Or, schedule a meeting directly:
Book on Calendly